Work orders are the driving force behind your maintenance operation. They provide energy to your team and facilitate the movement of work from point A to point B. So, this article will teach you how to master the maintenance work order, know the format for writing it, and also the process and procedures involved so that your business runs smoothly.
What is a Work Order?
A work order is a document that contains all of the details about a maintenance task and outlines the process for completing it. It may include information such as who approves the work, the scope, who is in charge of it, and the work plan.
Work orders are critical to the functioning of a company’s maintenance department. They assist everyone from maintenance managers to technicians in organizing, assigning, prioritizing, tracking, and completing critical tasks. When done correctly, allows you to collect information, share it, and use it to complete tasks as effectively as possible.
Although a work order and a work request sound identical, there are a few key differences between them. Non-maintenance personnel uses a work request to notify the maintenance team of a task. When equipment fails, a machine operator, for example, can send a job request. A maintenance manager reviews the job request and adds additional detail, schedules the assignment, and assigns it to a technician. The job request has been transformed into a work order.
So we’ll learn the procedure/ process of creating a word order format in six steps.
Work Order Procedure/ Process
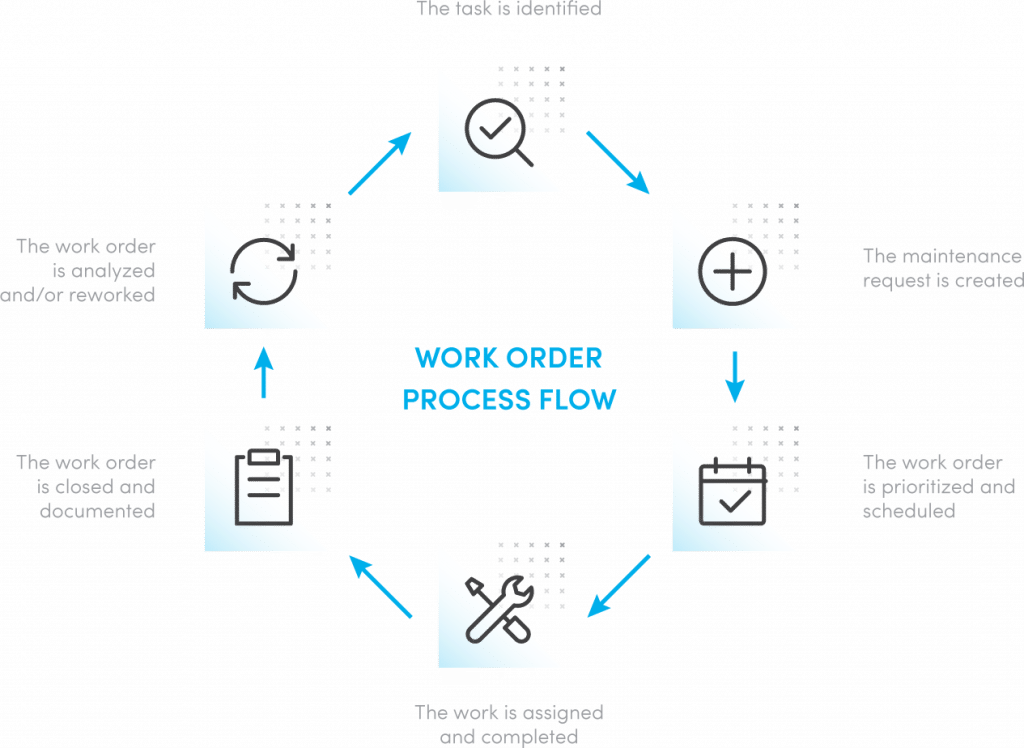
Any maintenance work order has a lifecycle that consists of three major phases: development, completion, and recording. We can divide these stages into several steps. Understanding each step and providing a solid work order process/procedure prevents projects from being stuck in one phase and becoming a backlog.
Step #1: Identify the mission.
Maintenance activities are divided into two categories: scheduled maintenance and unplanned maintenance. Anticipated maintenance includes all jobs that you know about ahead of time, such as regular checks, and unplanned maintenance includes all things that you can’t predict, such as an unforeseen breakdown.
Step #2: Make a repair submission.
Here, you compile the work descriptions and send them to the maintenance team for further action. If a computer fails, for example, an operator generates a job request and sends it to maintenance. When a job is scheduled, a work order is generated and activated at the appropriate time.
Step #3: Prioritize and plan the job order.
Most often, some occupations need more time than others. A burned-out light bulb may not need immediate repair, but a damaged conveyor belt can. That is why you must prioritize every work order that comes across your desk.
It is now time to plan after prioritizing. It may be coordinated based on a fixed date, expected maintenance triggers, or dedicated time blocks. Setting a deadline holds everyone responsible and also keeps everyone updated, ensuring that nothing slips through the cracks.
Step 4: Delegate and complete the job
It is now time to put those words on paper into reality. A technician is assigned to the job order and completes the mission. So, this can be as simple as a five-minute equipment check or as complicated as a multi-day repair job.
Step #5: Close and document the job order.
The work order will be closed until all of its terms have been met. Managers may be required to sign it off to meet enforcement criteria. When a work order is completed, it is tucked away. A well-organized work order log is essential for creating asset histories, evaluating previous solutions, planning for audits, and other tasks.
Step #6: The job order is reviewed
Reviewing work orders provides useful details. They will provide insight into your processes and systems that can be used to improve your company. The log also helps technicians to easily identify any missing steps or alternate solutions if a problem reoccurs.
Information for a Work Order Format
Generally, work orders, like anything else produced by your factory, must be well-made and also defect-free. If one step of the process is off, it can have an impact on the entire line. So, what information constitutes a great work order format?
- Asset: What piece of equipment requires repair?
- Problem description: What exactly is the problem? What did you hear, see, smell, or feel at the time of the failure or in the days preceding it?
- Work scope: What workforce do you need to complete the job? What abilities are required?
- Parts and equipment needed: Are there any parts that must be replaced or special tools that must be used?
- Notes on health and safety: What safety protocols and equipment do you need? Have any accidents or near misses occurred while working on a similar issue or asset?
- Date requested: When was the work order produced and submitted, as requested?
- Name/department/contact of the requester: Who created and submitted the work?
- Date expected for completion: When should this work be completed?
- Date of actual completion: When was the work finished and closed?
- Work hours expected: How long should it take to complete the work?
- Actual work hours: How long did it take to complete the work order?
- Task checklist: Is there a step-by-step guide to completing the required work?
- Priority: What is the significance of this work? Which is it: high, medium, or low?
- Assigned to: Who will be doing the work? Is it necessary to have more than one person? Is it necessary to hire an outside contractor?
- Associated documents: Are there any records that will help the work order be done more effectively, such as SOPs, manuals, diagrams, videos, asset history, purchase orders, or images?
Maintenance Work Order Management
Creating a fantastic work order format does not guarantee results. A solid format for handling a work order’s lifecycle ensures that it moves seamlessly from one stage to the next. This format allows you to escape a variety of issues in a work order, such as a lack of transparency, high costs, increased downtime, and a crippling backlog. So, let’s take a look at the advantages and disadvantages of a few job order management systems and how they compare.
Pen and Paper
Pros:
Work orders have been managed with pen and paper since the invention of the pen and paper. Written work orders are both economical and familiar. Also, paper is a method that everybody is familiar with. It requires very little preparation, the initial costs are relatively low, and there is a paper trail for when you need to review previous work.
Cons:
This system, however, has some serious flaws. Paper files are easily misfiled, misplaced, or destroyed. They are time-consuming to find, retrieve, and sort. Since we present reports are often after an event, inaccurate information is more likely to find its way onto a work order. Pen and paper are also being handled more slowly. These factors, when combined, render work inefficient and can cost you a lot of money in the long run.
Use of Whiteboards
Pros:
Another old standby for maintenance departments is whiteboards. The cost of materials does not exceed the budget, and it is certainly convenient to have all work orders available to view and update in one, central location.
Cons:
Whiteboards, like pen and paper, have significant limitations. Keeping records is a massive pain, and also extracting information from any records you may manage to obtain is incredibly difficult. This makes creating asset histories, preparing for audits, and creating work order reports nearly impossible. The management process is often slowed because operators and technicians must travel to a central location to send or display work orders.
Excel Spreadsheets
Pros
Excel spreadsheets are an improvement over pen and paper and whiteboards. It converts paper documents to digital format, making them less likely to be destroyed or lost. It is often simpler to scan for information and generate reports based on that information.
Cons
However, though spreadsheets lift the bar slightly, some factors make it an unsteady base for handling. Some spreadsheets are locked to a single screen, making it impossible to see the most recent details on a work order.
Spreadsheets, even though cloud-based, lack the ability to automatically trigger work orders, making preventive maintenance incredibly difficult to accomplish. Inputting data and making reports necessitate long periods of time at a computer as well as knowledge. There is also a limitation in tracking the progress of work orders, which puts you behind schedule.
CMMS (Construction Management System) Software
Pros:
The use of mobile and cloud technologies is one of the most significant advantages of computerized maintenance management systems (CMMS). This type of maintenance work order software enables anyone in maintenance to build, monitor, complete, and evaluate tasks in real-time, from anywhere—whether on the scene of a breakdown or a Hawaiian beach.
Work orders, asset histories, notes, and photographs can be brought with technicians everywhere they go. Reports also mine the data in maintenance work orders for metrics such as cost, efficiency, and others.
Submitting a work request through a CMMS can provide those outside of maintenance with a greater sense of ownership over that work. They can also track the status of their requests, and duplicate work orders. This is an important way to increase TPM at your facility and reduces the need for task updates or clarification.
Cons:
While CMMS software is the way of the future, it is more expensive upfront, requires exceptional training and culture to be successful, and frequently necessitates more advanced maintenance techniques. Though CMMS software has flaws, the system’s long-term benefits more than compensate for any initial shortcomings.
How can work orders help businesses ensure compliance with regulations?
Work orders can help businesses ensure compliance with regulations by documenting the completion of required tasks and maintenance activities, and providing a record of compliance for audits.
What is the role of a work order coordinator?
The role of a work order coordinator is to manage the creation, assignment, and completion of work orders, and to ensure that tasks are completed on time and within budget.
How can work orders help businesses improve customer service?
Work orders can help businesses improve customer service by providing a clear and organized process for addressing customer requests and tracking progress towards resolution.
How can work orders improve communication between departments?
Work orders can improve communication between departments by providing a centralized platform for documenting tasks, assigning responsibilities, and tracking progress, which can improve collaboration and reduce misunderstandings.
How can work orders help businesses with scheduling and resource allocation?
Work orders can help businesses with scheduling and resource allocation by providing a clear view of the work to be performed, the resources required, and the timeline for completion, allowing for more effective planning and allocation of resources.
How can work orders help businesses identify areas for improvement?
Work orders can help businesses identify areas for improvement by providing a record of completed tasks and the time and resources required, which can be analyzed to identify inefficiencies and areas for improvement.
Conclusion
Work orders are a cornerstone of excellent maintenance. When properly managed, they provide the team with the consistency and structure it requires to be successful.
A well-designed maintenance work order process/ procedure facilitates the establishment of a preventive maintenance program and the response to unplanned maintenance. So roles have been described, workflows have been improved, tasks have been monitored, and information has been well-documented.
The final and most important piece of the puzzle is selecting the best methods and processes/procedures for managing work orders. When all comes together, the operation will be able to master the basics of maintenance while still looking for new ways to expand and flourish.
Work Order FAQs
What is a work order in ERP?
A Work Order is a document given to the manufacturing shop floor by the Production Planner as a signal to manufacture a certain quantity of a certain Item. The Work Order also helps generate the material requirements (Stock Entry) for the Item to be produced from its Bill of Materials.
Is a work order an invoice?
A work order is a document that assigns a service to be completed for a customer. An invoice is a document that provides an itemized list of the services provided and the charges for each.
Why generate a Work Order?
The purpose of a work order is to initiate a task, clarify what is to be done, specify completion dates, and give special instructions as needed. CMMS work order management software also helps organizations manage and maintain data on projects as well as on resources, expenses, and labor.
How do you write a work order?
At the top portion of your work order is where you will write the following: The company name. The complete address. Essential contact information.
…
Once you have written the company contact details, include beside it the following:
- Work order number.
- Job number.
- And the inclusive date.